I’m posting this pic hoping it will help others with their ongoing mysterious printing issues, specifically the problems @rogermc has been experiencing here
I was planning on providing sufficient documentation along with any reveal-pictures of my MKII printer setup, but time is passing too quickly these days and I’m experiencing very tough days with severe pain from a car-accident many moons ago…so this picture is posted without supporting documentation. Heck, I was even planning an Internet Contest with many cool prizes along with the introduction of my collection of mods for this printer.
Interestingly, in the last post above, the photo of the Delrin belt-connector also shows another simple mod that increases print-accuracy when combined with other mods I’ve designed for the extruder assembly. I purposely set the camera-focus on that part instead of the Delrin connector
, you know…for the fun of it … and maybe even some aha moments for folks.
Improving/designing industrial and general consumer products has been an enjoyable focus for many decades, I’m not going to waste any of my time or yours discussing where I’ve been professionally to support my works. I’ll just say “I’ve kinda got-a-knack for a bunch-of-differing-stuff” 
Ok, enough rambling…
above: extruder motor adjustable in the vertical and horizontal, nozzle and heater-block adjustable in the vertical and horizontal, fan/duct assembly swings in all-directions. Rock-solid nozzle-mount provides for extremely accurate retractions, layer-height, layer-width and vertical alignment. The vertical position of the nozzle is one of the most important preventative maintenance tasks on-the-list of things-to-do for error-free and accurate printing. The round aluminum holding the nozzle also lowers the top-of-the-heat-zone in the nozzle. Securing, aligning and cleaning the nozzle is by-far the best things you can do to your printer in your quest for reliable/accurate prints from your Cetus. The filament you see loaded is Ninjatek Armadillow.
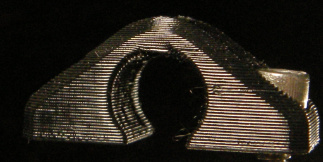
I just printed my first model with the Armadillow filament, the only problem I have is I’m experiencing too much temperature-swing …this filament has a very-tight temperature tolerance and is the reason why the photo above has surface artifacts and the bridging somewhat failed(among many other reasons)…while printing I had to turn the fan on-and-off repeatedly to keep the temp within the 4 degrees celsius tolerance needed for the quality I’m looking for.
The above photo is printed using 3 layer-heights, .30mm, .20mm and .10mm , 3 different layer-widths, .40mm, .50mm and .60mm respectively. There are also 2 different infill line-widths along with 2 different infill patterns. Using these settings has allowed for rigidity where needed, and extra vibration/frequency -dampening where needed on these extruder motor-mounts.
July5 add : Oh…the chamfer you see in the photo above only exists on this side, the other side is a 90degree edge… the chamfer works with some of the interior structures.
July6 add: you may notice the head of the socket-head screw, just to the right, in the rail, is closer to the surface of the rail compared to other rail fastener heads. This screw is 6/32" x 20mm long, the screws main function is to lessen the horizontal axial-torque in the extrusion. When you provide ultimate-strength stabilization to the nozzle assembly, z-axis tower and x-axis, you are now left with the lesser noticeable structural forces/variables governing print-quality…axial-torque and linear guide-block tolerances. The 6/32" x 20mm fastens the guide-rail to the other side of the y-axis extrusion arm…there are 3 locations I’ve employed y-axis axial-torque limiters.
These lesser forces are difficult to measure, they happen quickly and are not noticeable when they happen unless you use lasers to measure the movements. I have also found the effects of these forces on print-quality are less noticeable on thicker layer-heights of .30mm and above. I’ll try and prepare some visuals.
update: heating issue, solved …it’s been awhile since checking the heat-block thermal paste, re-applied a nice blob in each hole and re-inserted the heating components…back in business!
cheers and good journeys folks!